Copies of the Flights of Fact and Fantasy Proceedings where this paper was published are available for purchase from The Airship Association.
ABSTRACT
The transport of goods and personnel to locations that are not connected to the established transportation infrastructure imposes additional costs on economic development. The introduction of a new generation of cargo-carrying buoyant aircraft (airships and hybrid vehicles) could be especially significant to the economics of the mining industry in remote locations. While the volume of mineral concentrates to be transported could demand relatively large buoyant aircraft (greater than 50 tonnes lift), some aspects of the mining industry could benefit from the availability of the buoyant aircraft being developed that lift between 15 and 50 tonnes. In particular, mineral exploration drilling projects require short-term logistical support in this weight range. Moreover, buoyant aircraft could avoid some of the mitigation costs associated with the potential environmental damage and safety hazards created by current transport methods. This paper outlines the logistical requirements for exploration equipment movement and camp development using a stylized case model. The limitations of current practices are compared to the economics of buoyant aircraft and their associated advantages.INTRODUCTION
Mineral exploration projects in the Canadian Shield and Arctic Regions (CSAR) occur on claims that are frequently remote from established transportation infrastructure grids. A claim is an area of land in which a resource company holds mineral rights. Drilling equipment, provisions, temporary accommodations and people must be shipped to the claim in order to delineate it. Everything must be despatched from the end of the established all-weather road network across craggy terrain, swamps, muskeg, lakes and many water crossings to set up temporary exploration camps. When the exploration is complete, waste, people, core samples and equipment must all be returned and the drilling site restored to a natural state. To reach exploration areas beyond the all-weather roads, mining logisticians use trucks over temporary bush roads, “cat trains” (sleds pulled by skidders), helicopters and small floatplanes. As noted by one of the leading exploration companies, “The more easily accessible mineral reserves all over the world are being depleted.” [1] They go on to note that over the next 20 years, new deposits will be found only in the more remote areas. Figure 1 presents an illustration of the CSAR region with the approximate limits of the road and rail networks. The location of Baker Lake, Nunavut, which is the geographic centre of Canada*, illustrates how much of Canada is accessible only by air and/or marine transport. This area is without permanent infrastructure and accounts for about 70 percent of Canada’s land mass. The high logistics costs of reaching remote locations discourages mineral exploration. The purpose of this paper is to assess the competitiveness of a new generation of cargo-carrying buoyant aircraft in support of mineral exploration drilling projects in the CSAR.(*64 degrees, 18 minutes, 41 seconds N and 96 degrees, 4 minutes, 8 seconds W)
![Figure 1: Limit of land based transportation infrastructure in Canada [2]](https://nomadicminer.com/wp-content/uploads/2018/06/Fig1-Airship.jpg)
MINERAL EXPLORATION PROJECTS
Mineral exploration projects begin with geophysical surveys in the air or at ground level. The survey results may reveal the presence of out of the ordinary geological features, which are termed anomalies. If the anomalies are sufficiently promising to indicate that material of commercial interest could be present, a team may be sent out to prospect the claim directly [3]. The prospecting teams take samples from the anomalous areas noted in the surveys. These samples could be composed of rock, soil, till and lake sediment that are analysed to identify the presence of mineralisation. If the samples show promising degrees of mineralisation, further surveying, mapping and sampling may be conducted to define the anomaly. This work is largely based on helicopter transport.Drilling Exploration Logistics
If the analysed samples show mineralisation of commercially interesting material, higher impact activities such as drilling may then take place to further delineate the mineral deposit. The types of drilling include auger drilling that retrieves samples of soil, reverse circulation or rotary drilling that recovers chips of rock, and diamond drilling. Diamond drills penetrate the ground with a drilling head studded with diamonds that recovers a rock core which is cylindrical. The core is analysed to determine the extent of mineralogical content and the structural geological characteristics of the ground [4]. Diamond drilling is used most in the CSAR for mineral exploration. At the exploration drilling stage, it is often necessary to set up a camp on the claim where a team can be based to conduct the mineral exploration. This team would be comprised of drillers, geologists, mechanics, first aid attendants, and management personnel. The number and depth of drill holes planned during the length of the project affects the exploration team size. The characteristics of the camp vary depending on the size of the exploration team working at the camp and the weather. Typical camp infrastructure is shown in Figure 2. Infrastructure items would have to be transported to camps with the likely exception of water, which is often easily accessible throughout the CSAR. The logistics systems of the camp encompass four functional areas, namely living accommodations, nourishment of the crews, office service areas, and energy/waste utilities. The cycle of the camp begins with the slow build up by an advance group to organize the facilities. After camp construction, supplies and crew movements must be transported until the final decommissioning of the camp. The work schedules are managed to avoid seasonal impediments like the freeze-up and break-up of the lakes in the fall and spring.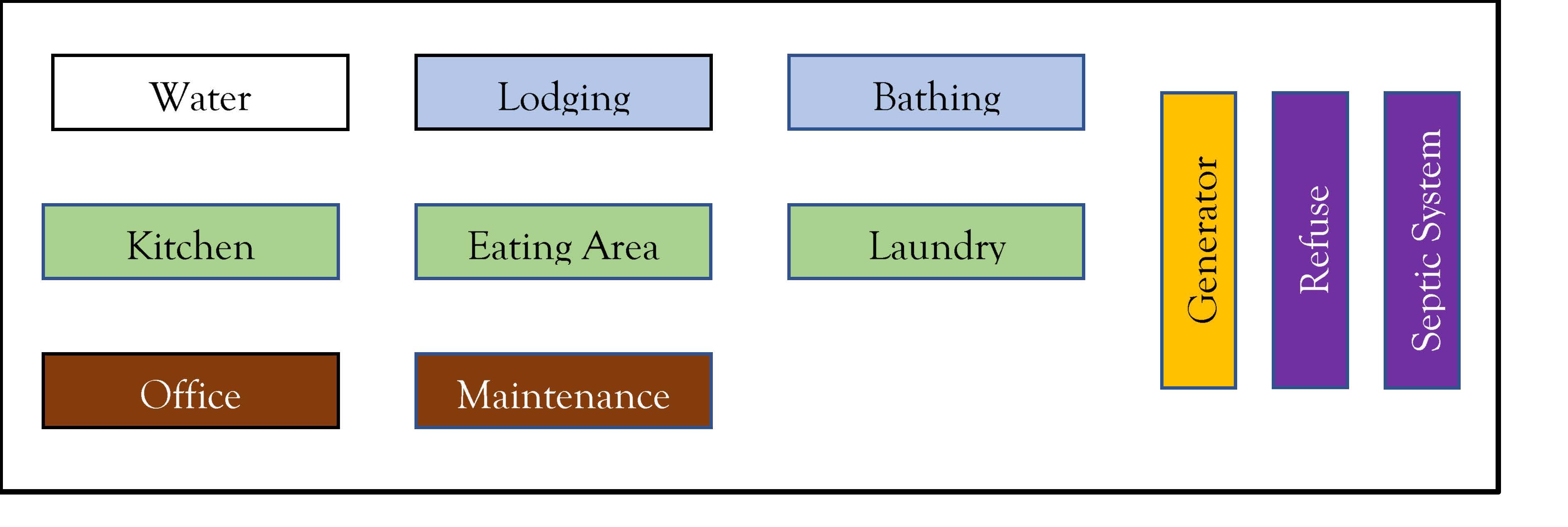

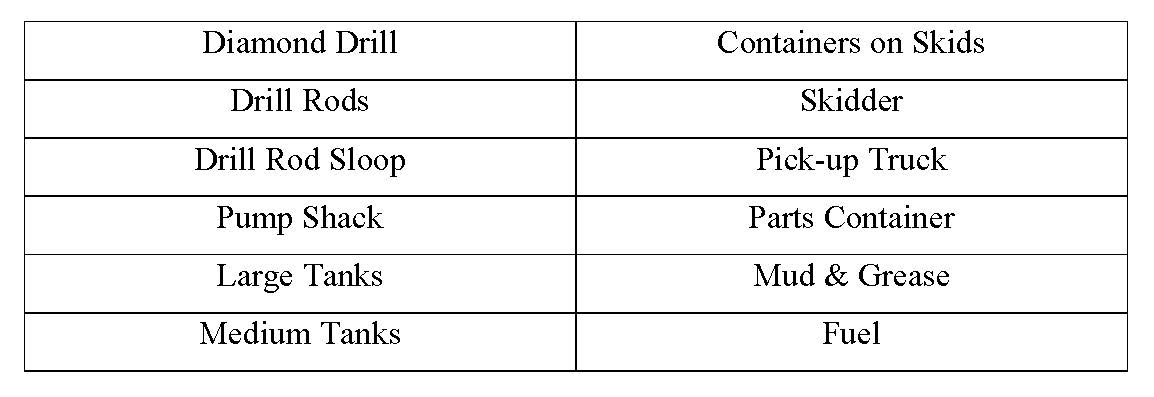
TRANSPORT COMPARISONS
The economic sustainability of using buoyant aircraft to support the logistics of a mineral exploration project is considered relative to the current logistics methods based on bush roadways and air transport. The existing logistics costs are described with a stylized model based on a hypothetical situation. Subsequently, the economics and operational considerations that confront the use of buoyant aircraft to serve the remote exploration drilling location are assessed.Bush Roadways
Constructing roadways through the bush impacts the environment. Vegetation removal and exposure of road surfaces can cause erosion [6, pp. 21-62], while vehicles disturb the ground and affect wildlife habitat. Constructing and shipping cargo on bush roads increases risk [5, pp. 712-714]. Working around powered mobile equipment in the bush increases hazards because of limited visibility. These roadways are narrower and curve around obstacles to save costs and to lessen environmental impact. This in turn poses additional risks when travelling on the road. Consultation with government and non-governmental organizations is required to obtain approvals. The weather conditions affect how these temporary roads are constructed and when they are ready to be used. Construction through the bush must be timed to ensure that the road is not boggy due to water from melting snow or rain. Muskeg and swamps can only be crossed when frozen. Roadways for vehicles to drive over ice-covered water bodies can only be used when the ice is thick enough. The load that the ice can support decreases when temperatures rise. Fissures may also be created between the ice surface and the water body that will not support vehicles. Bridges must be constructed over rivers and streams that are not ice-covered. Once the ice road is constructed, continuous testing is required and snow must be removed. The costs behind developing a temporary road from the established transportation infrastructure to a mineral exploration site must be factored into the total cost of the exploration project [7]. The investment in a temporary roadway would be made at the beginning of the first season of a project. However, the roadway route may be altered from season to season if the mineral exploration site locations on the claim or environmental conditions change. There are also road maintenance costs that would be incurred while it is being used.Air Transport
Conventional air transport includes aeroplanes and helicopters. Air transport in remote areas is often done with floatplanes because they can land on the water bodies. Docks must be constructed when float planes are used. Construction of a roadway to the mineral exploration project is required to access the landing areas. This adds cost that may only be justified if it is a multi-year exploration site. Ice runways can also be constructed on lakes during the winter to replace the floatplane service. In the Arctic*, it is common to see an older Boeing 737 jet aircraft serving exploration camps. Ice runways are more practical in the Arctic than in the Canadian Shield because colder temperatures permit their use for a longer period of time. Also, ice conditions are adequate to transport equipment for a longer period of time in the Arctic than in the Canadian Shield.Helicopters are used widely in mineral exploration. They are used almost exclusively in mountainous regions. Landing spots have to be constructed but these are generally small and not overly expensive. The main climactic conditions that affect aeroplanes and helicopters are wind, fog and icing. At certain times of year (freeze-up and breakup) floatplanes cannot operate, and in general these are down periods in the exploration cycle. Although aircraft transport is safe, unsafe acts could be catastrophic to the aircraft and all those within the aircraft as well as those people on the ground [5, pp. 469-507]. Considerable regulatory oversight is imposed on all air operations. Aeroplane and helicopter transportation costs are high. Using helicopters to transport loads costs more than aeroplanes, but they can carry slung loads that will not fit though the aeroplane door. Helicopters are also needed to move equipment like drilling machines around the exploration site where snow is not available for sledding. This is frequently the case in the Northwest Territories. Larger aeroplanes can offer lower costs per kilogram, but longer and more substantial runways must be built if the aircraft size is increased.(*Arctic approximately from 66° 33′ North of the equator to the geographic North Pole)
Buoyant Aircraft Transport
Buoyant aircraft could provide a desirable alternative means of transport for mineral exploration projects. Prentice and Knotts [8] provide a survey of worldwide competition to develop cargo buoyant aircraft. Many design alternatives are being considered based on structure, buoyancy control and cargo exchange method. At this point, a dominant design has yet to emerge, but it now seems to be only a matter of time. This paper makes no effort to assess which type of buoyant aircraft is best suited to mineral exploration activities, except to note that autonomous landing and ground handling is likely imperative given the short duration of drilling projects[9]. Given the relatively large size of buoyant aircraft cargo bays, over-sized and awkwardly shaped pieces can be carried. Buoyant aircraft have the ability to land on water or in a relatively small cleared space. The surface does not need to be built to the standards of a gravel runway used by aeroplanes, but the ground needs to be relatively level and free of trees. In most cases, a water-based landing area would likely be preferred. Gateways within Canada from where the buoyant aircraft can leave to access the CSAR are shown in Figure 3. All these locations are accessible by road except for Baker Lake, which is used as a point of reference. Of course, access to drilling sites from the coastline would be possible for a buoyant aircraft-marine service in many regions of the North during the summer and early fall.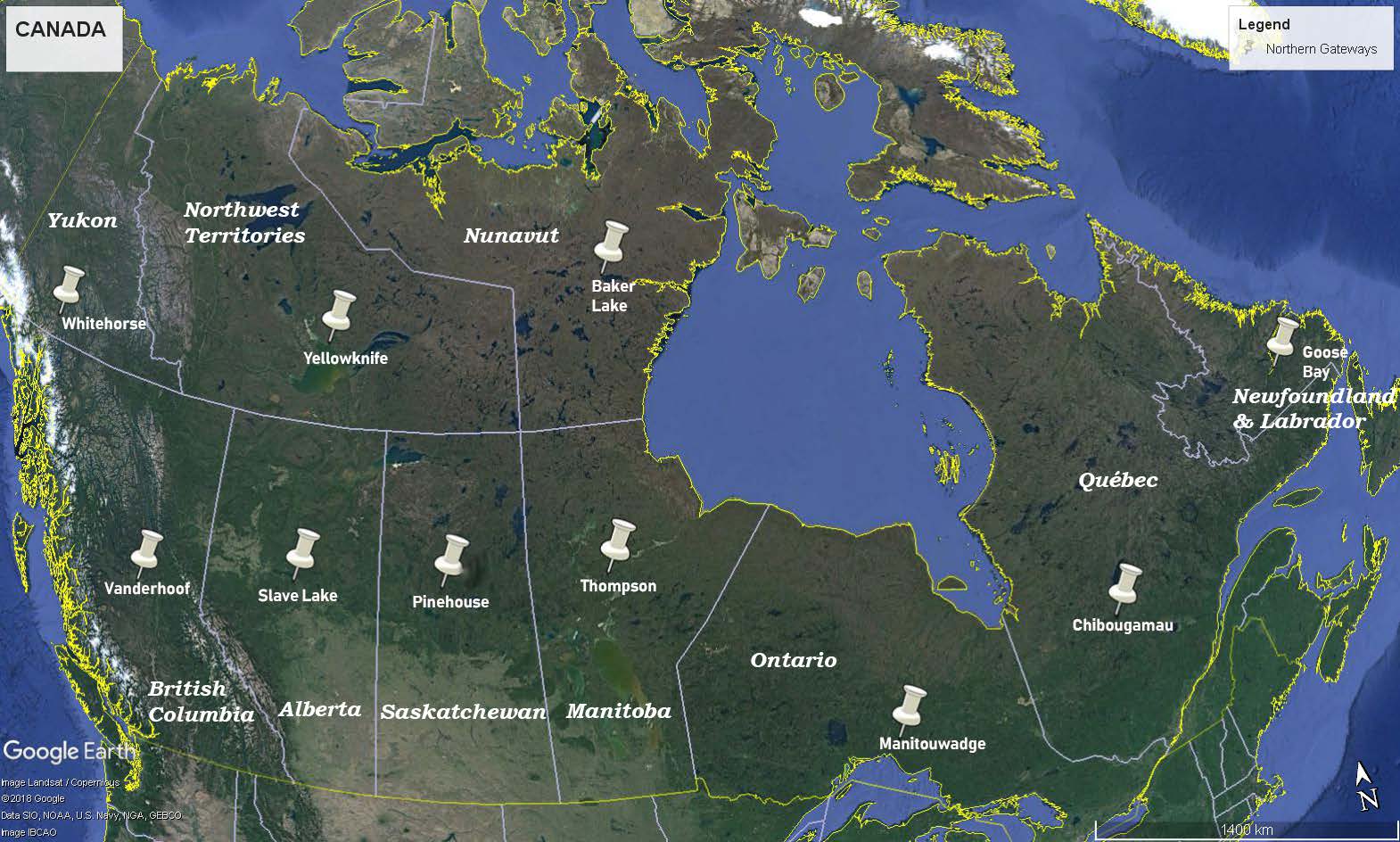
Stylized Case Study
A stylised model of a representative project is used as the base of analysis because the circumstances in which drilling activities operate vary greatly across Canada’s land mass. The model exploration mission described here involves a one-year drilling operation. Such projects could be extended over several years, but the contracts are typically year-to-year. Figure 4 presents a topographical map of Canada. The experience described here would not applicable to mountainous areas or sea coasts. As stated before, diamond drilling in the Rocky Mountains is almost exclusively done with helicopters. Most coastal projects involve some sea movement, although this analysis would be similar for the land portion of these projects. Most of the drilling projects in the CSAR involve a bush-road/air combination, or air-only logistics.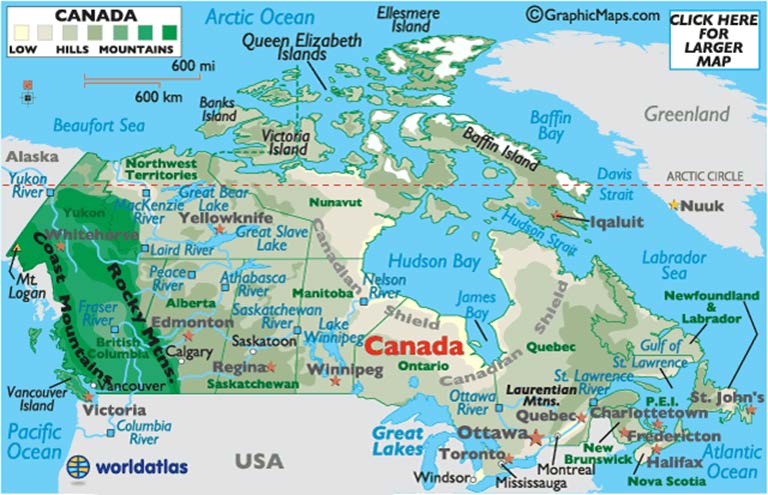

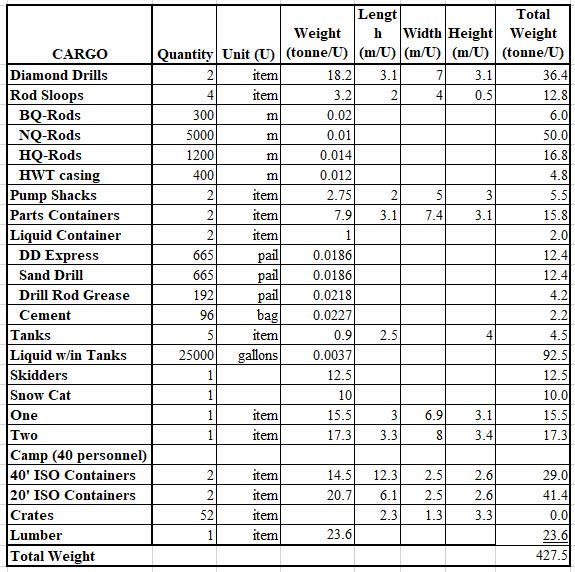
However, this would only be done if the drilling project extended beyond one year. In a one season project, the drills would come out in April with other materials and supplies. It is worth noting that with a project with a 185-kilometre access road, it is more likely to be a multi-year project. The costs in the second and third years would be less because the system would only be re-opened, and some equipment would not be returned to a transportation grid from the mineral exploration project until the end.*Approximately the 8th of February to the 7th of April.
Economic Analysis
At 20 tonnes per truck, it would take 24 trucks to move the 475 tonnes for this stylized exploration project. Similarly, it would take 24 trips by a 20-tonne lift buoyant aircraft to serve this project. Using an average cost of $.50 per kilogram, the buoyant aircraft would cost $237,500 in total, or about $10,000 per trip. In comparison, the road for this project would cost approximately $500,000 and the trucking could add another $50,000 for a total of $550,000. Of course, some allowance must also be made for demobilizing the camp and bringing out core samples. Presumably, this would involve fewer trips, but even if the cost of the buoyant aircraft were doubled, it would still be more economic in this example. The competitiveness of buoyant aircraft depends on the length of the road. The majority of the trucking cost is road construction, and this is a linear function of distance. A conceptual model of the economic trade-off between trucks over bush roads and frozen lakes, and buoyant aircraft is presented in Figure 5. Unlike permanent roads that have a long-term capital value, temporary roads over lakes and bush can be treated as variable costs. The model considers the costs of building roads and operating trucks over various distances. For short distances of perhaps 50 km or less, bush roads and trucks are likely more economic than buoyant aircraft in direct transport cost terms. For longer distances, the buoyant aircraft could have lower total cost. More research is required to define these competitive ranges.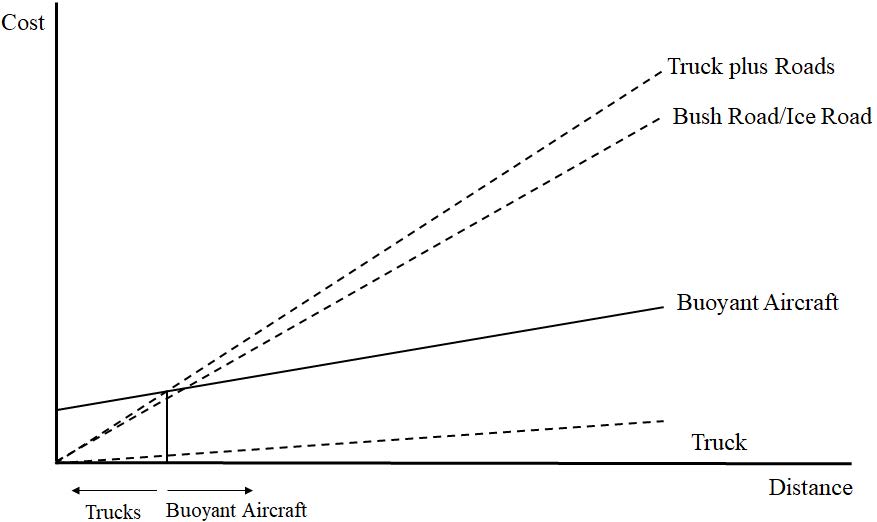
Conclusion
Continuous exploration is necessary to maintain the reserves of mineral deposits that are needed to support an expanding world economy. As stated by Mark Bristow, CEO of Rangold Resources: “It is misguided to think that cutting back on exploration is a good idea, because it creates the most value … True value is found at the drill bit …” [1] The problem that confronts the mining industry is that exploration costs are increasing. As mineral deposits in conveniently located areas are exhausted, the mining industry is forced to search in more remote and inaccessible areas of the Earth. The sheer cost of exploration in remote areas can constrain mining companies from studying anomalous areas identified by geophysical surveys. As existing mineral reserves are exhausted however, access to more remote locations for development is necessary. Conducting mineral exploration projects in inaccessible areas like the CSAR is challenging. In most cases, these projects require the construction of a temporary road through undisturbed territory. These roads do not get much utilization because exploration may be limited to the winter season when frozen lakes and swamps can be negotiated. Mineral exploration projects can avoid the costs of road construction by using aeroplanes and helicopters to reach the mining claims. However, the cost of conventional air transport is much higher and less convenient because larger equipment must be disassembled for transport. Transporting cargo to mineral exploration projects from established infrastructure using buoyant aircraft has a number of advantages. This is particularly true for locations that are farther from existing transportation gird because temporary roads have no salvage value or on-going use. The direct environmental impact of blazing a trail through undisturbed natural areas could be eliminated if buoyant aircraft are used. In addition, the risk of spills or accidents on the ground is minimized because less work has to be conducted around heavy machinery. Driving on ice roads over frozen lakes is another safety risk that would not be present with buoyant aircraft. Although it is difficult to put monetary values on environmental and safety issues, costs are certainly incurred by companies on inspections, permits, training and management to mitigate these risks. Buoyant aircraft could increase the flexibility of constructing exploration camps and accelerate the development of mines. The length of time ice roads can be driven on varies depending on the weather conditions from season to season and year to year. Buoyant aircraft can be used year-round and are not confined to separate seasons. At the present time, it takes 10 to 15 years to bring a mine from exploration into production. Any reduction in this time will have a significant monetary benefit. Many remote destinations in the world could use buoyant aircraft for mineral exploration projects. Depending on the volume of exploration work being done however, it might be difficult to get sufficient annual utilization of the buoyant aircraft to justify its capital cost. The solution could be to combine shipping to mineral exploration projects with other transportation activities. These could include shipping supplies to remote communities, assisting the development of capital projects, like roads, and transporting provisions to and from operating mines. The ground-handling of a cargo-carrying buoyant aircraft is yet to be demonstrated in commercial use. The least cost option for mineral exploration in the CSAR would be to land on a body of water or a flat marshy area. It is unclear whether or not the buoyant aircraft could land on such surfaces during the freeze-thaw cycles, but these are relatively short periods. If a landing pad must be constructed this will add to the cost. At this stage in the development of a new generation of buoyant aircraft is it impossible to be too definitive in terms of cost comparisons. What does seem obvious is that buoyant aircraft are better suited for transportation to remote projects than the conventional means of access by land or air. The suitability of buoyant aircraft increases the more remotely located these projects are from the transportation grid. Whereas the costs of building land access increases in direct proportion to distance, the incremental costs of distance are relatively low for buoyant aircraft. However, these are not inexpensive machines and they do require high rates of utilization to keep their costs down. The best-case scenario is for mineral exploration projects to be a complimentary service provided in conjunction with scheduled transport resupply to remote communities and operating mines.References
- [1] Major Drilling, Major Drilling – Quality • Safety • Results, Moncton, NB, 2017.
- [2] H. Panebaker, “Canadian Shield,” 8 March 2017. [Online]. Available: http://www.thecanadianencyclopedia.com/en/article/shield/. [Accessed 26 October 2017].
- [3] Directorate, Minerals & Petroleum Resources, “Stages of Mineral Exploration & Development,” Indigenous & Northern Affairs Canada, 2010. [Online]. Available: https://www.aadnc-aandc.gc.ca/eng/1100100023711/1100100023713#chp1. [Accessed 24 7 2017].
- [4] N. W. Byrne, “Diamond Drilling at Lake Athabasca,” CIM Bulletin, vol. XL, pp. 165-184, 1937.
- [5] Prospectors & Developers Assocation of Canada, “e3 Plus: A Framework for Responsible Exploration – Excellence in Health and Safety e-toolkit (EHS) Version-01,” 2 3 2009. [Online]. Available: http://www.pdac.ca/priorities/responsible-exploration/e3-plus/toolkits/health-and-safety. [Accessed 25 7 2017].
- [6] Prospectors & Developer Association of Canada, “e3 Plus: A Framework for Responsible Exploration – Excellence in Environmental Stewardship e-tookit (EES) Version-01,” 2 3 2009. [Online]. Available: http://www.pdac.ca/priorities/responsible-exploration/e3-plus/toolkits/environmental-stewardship. [Accessed 25 7 2017].
- [7] B. E. Prentice, N. Grenwal, B. Doell and M. Adaman, “Cargo Airships Versus All-Weather Roads – A Cost Comparison,” in Canadian Transportation Research Forum, Halifax, Nova Scotia, 2013.
- [8] B. Prentice and R. Knotts, “Cargo Airships: International Competition,” Journal of Transportation Technologies, vol. 4, pp. 187-195, 2014.
- [9] B. E. Prentice. and S. Ahmed, “Ground-Handling Systems for Cargo Airships,” in Canadian Transporation Research Forum, Winnipeg, Manitoba, 2017.
- [10] “Encyclopedia of BC,” [Online]. Available: http://knowbc.com/var/knowbc/storage/images/books/encyclopedia-of-bc/p/physical-geography-of-bc/maps/figure-7-physiographic-regions/38535-1-eng-GB/Figure-7-Physiographic-Regions.gif. [Accessed 26 October 2017].